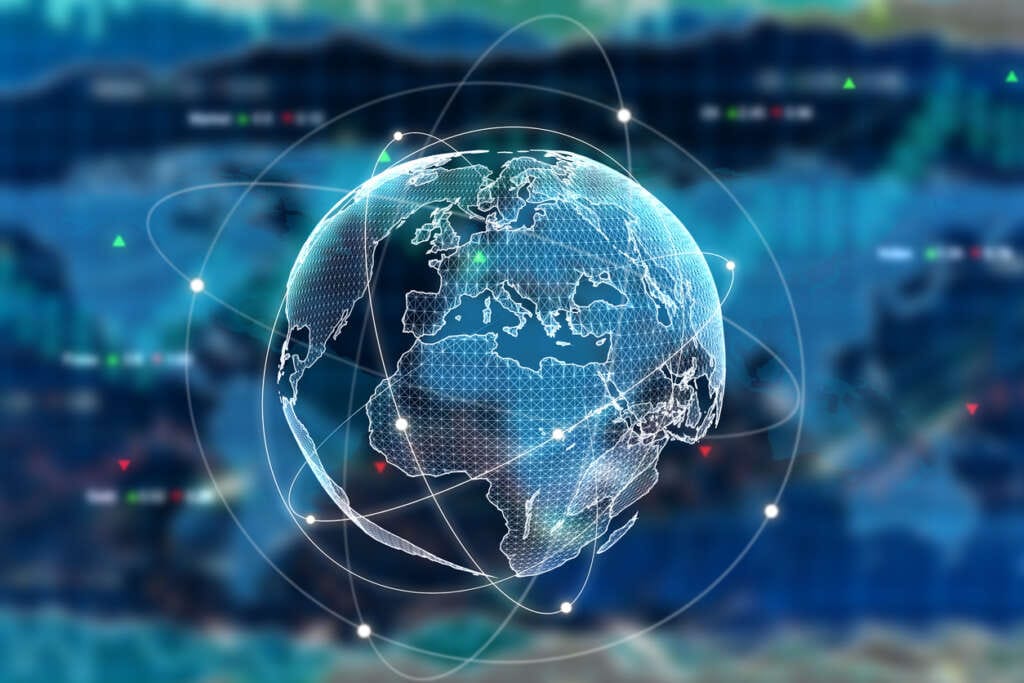
By Andrew Newton, Dynamics 365 Business Central Food Consultant at Columbus UK
Supply chain issues are typically only discovered during times of crisis – witness the disruptive period for the manufacturing industry following Brexit and COVID-19 . Now, as world economies reopen, demand for energy, labour, and transport has skyrocketed, putting pressure on just-in-time, cross-border supply chains to keep warehouses open and shelves fully stocked. With disruptions lasting a month or longer happening every 3.7 years on average, Andrew Newton, Dynamics 365 Business Central Food Consultant at Columbus UK, explains how long-term digital transformation with AI and predictive maintenance playing a key role, can help manufacturers create resilient, flexible and efficient supply chains.
When the Ever Given vessel got stuck in the Suez Canal back in March 2021, it showed the true impact a single event can have on the entire global supply chain. But today’s manufacturing companies must now also contend with lorry driver shortages and the economic consequences of price inflation, alongside drastically changing customer expectations and short-term shopping fads –demonstrating just how vulnerable and less reliable current supply chains are.
Key players within the manufacturing industry have all been impacted by supply chain disruptions to varying degrees of severity. The damage is clear. Inefficient supply chains can be a crippling economic burden, with hidden costs that are difficult to quantify. In many cases, manufacturers just don’t have the end-to-end visibility of their supply chains to make them aware they even have a problem. Rising transportation and warehousing costs, increased capital tied up in inventory and unhappy customers are quite often the first warning signs, but many manufacturing companies are still not set up to take corrective action.
As supply chain disruptions become part of the new business environment for manufacturers, it’s time for them to stop relying on disparate and siloed operations– and digitalisation holds the answer. In particular, innovative technologies from AI to predictive analytics tools can help manufacturers future proof supply chains from widespread disruption.
- Master planning with traffic light ratings will strengthen supplier networks
In the current environment, concern around product sourcing is at an all-time high with many businesses considering a shift to local suppliers. Kellogg’s for instance managed to quickly source a new supplier closer to home to overcome disruption in the early months of the pandemic – but with technological assistance, supply chain flexibility can be more than a one-off reactive shift.
Supply Chain Management software with inter-company functionality can set up traditional relationships between manufacturing, distribution and retail companies. It can also configure master planning so that sales demand created within one company automatically passes through the supply chain to the final source of supply. This enables manufacturers to incorporate new requirements in order to build supply chains back for the varying demand.
An ERP system with an integrated business intelligence tool, such as Power BI, allows manufacturing companies to create a dashboard focused on suppliers and customers, along with clear traffic light ratings. This makes it easy to identify areas of greatest risk, share this report with anyone who needs to access it and address potential weak points in the supply chain before disruption can destabilise operations.
- Keep your finger on the supply chain pulse with warehouse management and a smart factory setup
Efficient warehouse management can help manufacturers prevent product shortages during times of increased demand and, at the other end of the spectrum, having too much ‘dead stock’ – and this is where data intelligence can play a key role. IoT and AI devices can receive real-time data on the capacity and consumption of goods, providing manufacturers with the end-to-end visibility to stay on top of stock availability and capacity constraints caused by new customer demands.
Technology can even act as a supply chain safeguard against less expected changes. For instance, manufacturers can create system alerts with Supply Chain Management software and heatmaps of warehouse processes to flag exceptional supply chain situations. This could be for circumstances such as product inventory levels that are below target minimums, or actual supplier lead times that exceed those planned, to help businesses improve on-time delivery and customer experiences.
- Optimise production performance by keeping track of outside pressures
On the production line, technology can provide a greater level of connectivity, especially when it comes to automated operations. For instance, manufacturers can replace manual processes with ERP systems to receive automatic updates on equipment performance and more easily keep up with regular maintenance. This boost in workforce productivity and equipment efficiency can significantly increase uptime, throughput and quality.
But keeping track of outside pressures is key. Mixed reality technology and predictive analytics tools can make it easier to manage resource use and product standards. AI and Machine Learning (ML) tools for example can keep track of market trends, making it easier for manufacturing organisations to anticipate potential shifts in customer demand and raw materialavailability.ERP systems with flexible planning and forecast models on the other hand, are also beneficial for businesses in the manufacturing industry. Forecast models can take into account current and historical weather patterns, allowing manufactures to accurately base production cycles.
AI and ML tools also allow manufacturers to monitor aspects such as environmental and ethical risks associated with the supply chain. This capability is particularly important with the rise of ethical consumerism, which globally has seen 93 percent of consumers expecting brands to take action on local, social and environmental issues.
Take the digital leap to avoid the ‘butterfly effect’ on future manufacturing supply chains
In today’s volatile environment, manufacturing businesses must act fast to address supply chain issues before they lead to widespread disruption. Effective supply chain management involves having access to accurate up-to-date information regarding the demand and supply situation from an inside perspective and from the bigger picture of the global supply chain as a whole. Data needs to be presented in an easily digestible form – and digitalisation must become part of the solution. ERP systems, AI and ML technologies have the power to provide access to real-time data both inside and outside your company. This is how manufacturers can create world class supply chain networks and safeguard customer and business interests.