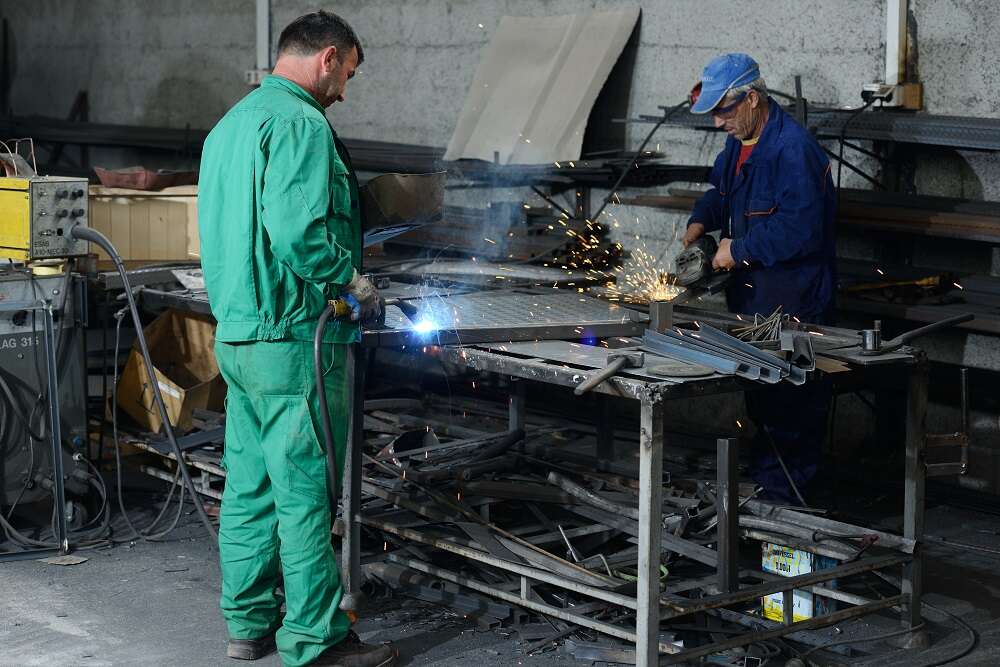
By Robert Merlicek, APJ CTO at TIBCO
In Australia, manufacturers are being offered some significant government support as they seek to leverage technologies like artificial intelligence (AI) and automation to digitally transform their facilities and processes.
Under its Modern Manufacturing Initiative (MMI) the Federal Government announced in August $800 million in co-funded grants for large projects to help Australian manufacturing businesses collaborate, innovate and build economies of scale. It is the largest component of the $1.5b MMI program designed to support Australian manufacturers to scale-up, build resilience and become more competitive, according to the Minister for Industry, Science and Technology Christian Porter.
The funding is certainly welcome, however there is still scope for Australian manufacturers to become globally competitive. This includes critical skills to enable them to effectively leverage the potential of digital technologies and data. There are a number of initiatives aimed at boosting the pool of skilled workers, but these will not deliver in the short term.
Manufacturing facing a skills challenge
In May, the IBSA Group, a not-for-profit organisation in the vocational education and training (VET) sector, released a report, Scaling Up: Developing Modern Manufacturing through a Skilled Workforce. It summarised a series of consultations, hosted by IBSA, in which manufacturing stakeholders from across the sector discussed the skills challenges and opportunities. The report said skills development was essential to underpin a vibrant modern manufacturing industry in Australia. In particular, it identified the need for new skills to support new manufacturing technologies like robotics, digital twins, and remote monitoring of automated facilities. It concluded that ensuring an adequate supply of skilled workers and maintaining currency of workforce skill would be challenging.
Meanwhile, Australian manufacturers need to respond immediately to today’s challenges, and a very effective way is to become more data driven, with tools to gather and analyse data generated by and available from their current operations.
Leveraging the power of data
Australian manufacturers need a strong digital foundation that underpins all aspects of their operations: operational resilience based on next-generation analytics and artificial intelligence (AI) that can provide insights into suppliers, customers, connected machines and network partners to create a more resilient smart manufacturing supply chain.
A supply chain has to be flexible enough to absorb shocks, major or minor. These could be the result of natural disasters, unpredictable demand, or a pandemic. According to IDC FutureScape, extended visibility into its supply chain can reduce the impacts of supply side disruptions on a manufacturer by 50 per cent.
To create a resilient supply chain, manufacturers need responsive and resilient risk management operations capabilities, one that leverages platforms that support applied analytics, artificial intelligence, and machine learning. And they need trusted data, integrated from multiple sources that span the entire supply chain.
These sources need to include data from procurement and inventory management, finance, logistics and planning, operations, quality assurance, sales, and customer service
By applying AI and advanced analytics to this data a manufacturer can highlight the most critical lower-tier suppliers, create a supplier risk assessment, understand production capacity, estimate logistics capacity, determine the required supply, understand financial or liquidity issues and plan for customer demand.
For example, US company Hemlock Semiconductor, producer of polycrystalline silicon for semiconductors, was looking for ways to innovate to remain competitive in the global industry. The company couldn’t afford to allow slow decision-making and production bottlenecks to hinder any aspect of cost optimisation. It deployed a data analytics system that gives it insight into its manufacturing processes to better understand and quantify the impacts of temperature, pressure, and energy usage in the reactor process. This real time data and analysis enables teams to come together to solve problems and perform root cause investigations.
This is Connected Intelligence. It enables organisations to gather data from multiple sources to help decision-makers predict events and automate processes. It gives visibility into processes and operations without which is it difficult to make improvements, to know where and how to act to best improve and optimise operations.
Resilient, smart supply chains backed by technology-led operations capabilities are the future and can empower Australian manufacturers to intake data and evaluate risks associated with unforeseen events. Today, everything is connected and so manufacturers must access data and apply AI to their data to reap the benefits of real-time decision-making and automated action that will benefit their businesses into the future.