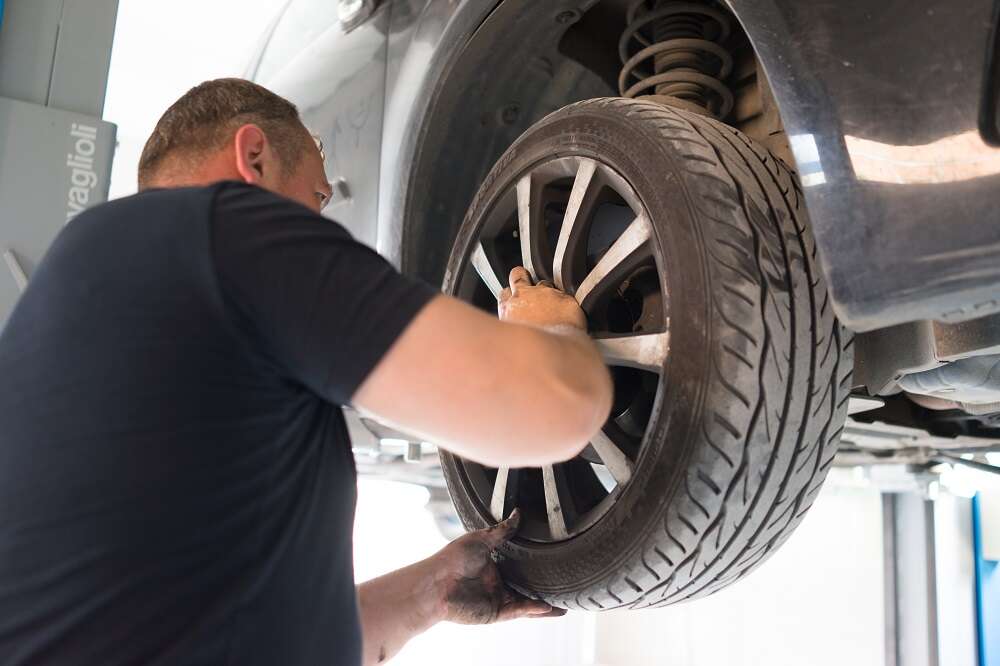
In this article, Mark Barclay from PartsForAllCars.com shares his insight into the effects of COVID-19 on the automotive industry — and what that means for the future of car manufacturing.
The pandemic has transformed every industry in many ways, whether that’s directly or, in the case of the automotive industry, by exacerbating existing problems. Even before the COVID-19 crisis, this industry was poised to take on major disruption from the introduction of driverless cars, the rise of electric vehicles, and the continued automation and use of robotics in manufacturing.
While it’s been a difficult few years for the automotive industry, it’s possible that already being braced for change is why responses to the effects of the pandemic have exceeded expectations, and vehicle manufacturing plants have shown remarkable resilience during the pandemic.
Despite the industry staying afloat, it’s safe to say that manufacturing processes have changed — perhaps even for good. Below, I’ll highlight some of the ways car manufacturing has been impacted by COVID-19, as well as how production and the rest of the supply chain is managing its recovery.
Health and safety in the workplace
COVID-19 has made us all more aware of health and safety in the workplace, particularly when it comes to cleanliness and PPE. But all points along the supply chain have also suffered from decreased productivity due to social distancing and other measures. For example, factories may be operating at a reduced capacity as they limit the number of staff that can be onsite at a time. Or, businesses may have to shut down plants more regularly for cleaning and hygiene purposes.
That’s not to mention the cost of these additional measures, such as the provision of mandatory PPE for all staff. For an industry with an already delicate economy, these kinds of changes can make a big impact in terms of output. On the plus side, manufacturing has adapted quickly to these necessary changes, and many of the adjustments that have been made to reduce the spread of COVID-19 benefit employees as well as employers.
It’s also important to note that while serious COVID-19 cases may be slowly declining thanks to progressions such as vaccinations, it’s anticipated that measures such as social distancing and mask-wearing will be required for the foreseeable future. So, what we have learnt to live with in 2020 and 2021 will continue to be part of our working lives for a long time to come.
Manufacturing and shipping issues
Automotive manufacturers and their supply chains have faced significant challenges including low sales, as retail stores have been closed during lockdown, and the population has stayed at home and travelled less. Financial stability among the general population may have also caused demand for new vehicles to drop. This is in addition to manufacturing interruptions as a result of workplace shutdowns and furlough schemes.
What’s more, the industry has faced further challenges with widely reported materials shortages, not just as a direct result of COVID-19, but because of factors such as international trade issues and problems with microchip supply. Key parts shipments, particularly from China, have faced massive delays, and in the UK, Brexit and new emissions targets have caused further disruption on top of the pandemic.
Fortunately, rapid digitalisation accelerated by the pandemic has helped car manufacturers to work more safely while increasing productivity.
How digitisation and automation are aiding recovery
Innovative technologies such as VR and simulation software can assist with product development, testing, and problem-solving. This allows for better — and often more productive — long-distance collaboration between teams that are working remotely.
Digital is also driving greater transparency in manufacturing, which can allow for more efficient output and management of resources. For example, the supply chain has greater insight into the processes and inventories of retailers, warehouses, and, most importantly, suppliers — including raw-material suppliers.
Now, inbound and outbound deliveries can be more routinely tracked across the supply chain, and with greater ease too. This allows manufacturers to forecast problems ahead of time and gives them the opportunity to address issues with more accurate solutions.
In short, digital can improve long distance communication, streamline processes, and allow for better resource management. So, the industry can not only overcome the challenges it has faced as a result of the pandemic, but it can continue to streamline its processes permanently in the future.
Impact on the future and the wider automotive industry
As both consumers and the industry focus on digital systems, electric vehicles, and other trends such as sustainability, manufacturers will also have to take these into consideration when it comes to the key skills of their workforces. Adjustments may need to be made to employ more software engineers rather than mechanical engineers, but to avoid lay-offs, businesses should consider upskilling or retraining their staff.
Other aspects of the industry, such as car parts retailers and mechanics, will have to adapt too. The pandemic has exacerbated the rise of electric vehicles and driverless cars, so these shops will have to adjust their inventory accordingly, stocking more electrical components such as batteries to cope with increasing demand, plus training staff to fit and fix more electrical components and software.
These are just some of the ways the automotive industry has had to adapt to COVID-19, and how manufacturing may look in the future as a result.